Resistance flash welding
Welded elements arranged so that they touch the end faces. In the process of butt welding spark can be divided into the following steps:
- preheating,
- sparking-out
- upsetting.
Heating is performed at low pressure. After the connection is warmed, there is a stage of sparking out, in which material of connection surface is fired, thereby resulting in a smooth, clean surface. When allowance for the sparking out is removed, there is a step of swell, wherein we get outflow of molten and oxidize metal.
Welded items are fixed and pressed in the jaws of welding and tightened by a little presure, which provides a contact at a few places. After switching the current flow through the contact areas with a small area and high contact resistance of the current flowing high density, causing melting of the metal contact areas, the creation of liquid bridges and rapid current burst them by the action of electromagnetic forces and the metal vapor pressure. Along with throwing liquid metal bridges of the contact area are removed at the same time any contamination. Advancing at a suitable speed, continuously, sparking process causes the heat from forming bridges ever new current flows into the welded objects and heats adjacent areas of the state a strong plasticization.
RESISTANCE FLASH WELDING PARAMETERS:
- current,
- sparking-out speed in mm/s,
- allowance for sparking-out in mm,
- swelling speed in mm/s,
- pressure strenght in kN,
- allowance for swelling in mm,
- clamping length in mm,
APPLICATION:
Resistance flash welding is used to connect the butt tubes, wires, rods sections, rails, tapes, sheets, cell chains, cutting tools, shafts, etc. welded items made of carbon steel, low-alloy, high alloy, copper and copper alloys, aluminum and its alloys. It is possible to combine steel with copper, copper, aluminum, low carbon steel with tool steel. Resistance welding spark allows you to connect objects with cross-sections of steel more than 100000 mm2, aluminum and aluminum alloys to 90,000 mm2, copper and copper alloys to 30,000 mm2.
MAIN ADVANTAGES OF SPARK-WELDING COMPARED CIRCUIT-WELDING:
- greater strength and plasticity of links
- a wider range of possibilities welding together of different metals (sparking period can last as long as each of the metal reaches the melting point)
- simpler to prepare items
- lower energy consumption and higher welding speed and therefore greater efficiency
- narrow heat affected zone

clients
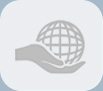
Manufacturers of fencing panels
A large number of customers of our machines are manufacturers of modern and practical modular fences...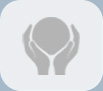
Manufacturers of gabions
New, interesting direction of development of small architectural elements, are gabions...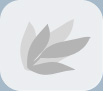
Manufacturers of welded screens
Screens are manufactured by using resistance welding of profiles with crosspieces or longitudinal wires with cross...Read more
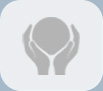